3D printing hasn’t turned out to be the replacement for injection molding that was promised but the technology is having an impact. Digital twins could be the secret to magnifying this impact.
Digital twins can improve product quality and process monitoring while making manufacturing cheaper. In this article, we’ll look at the potential future of digital twins in 3D printing. We’ll examine the motivation for developing the technology and the positive effects it could have on 3D printing processes and outputs.
Overview of Digital Twins
Digital twins are computer simulations of physical entities that capture actual or theoretical states of their physical counterparts. They achieve this thanks to physics-based models, real-time sensor information, historical data, probabilistic simulation, artificial intelligence, etc.
The Concept and Naming of Digital Twins
David Gelernter is often credited with introducing the idea of digital twins in 1991 through his book, Mirror Worlds. Just over ten years later, the basic concept was solidified by Michael Grieves and John Vickers. At the time, it was referred to by the less-catchy name, ‘Mirrored Spaces Model’.
In 2010, the term digital twin was finally introduced to NASA by Vickers.
Due to technological limitations, it wasn’t until the 2010s that the development of digital twins truly kicked off. Since then, they have been developed and used in many industries including aerospace, manufacturing, healthcare, and energy.
Digital Twinning Before 1991
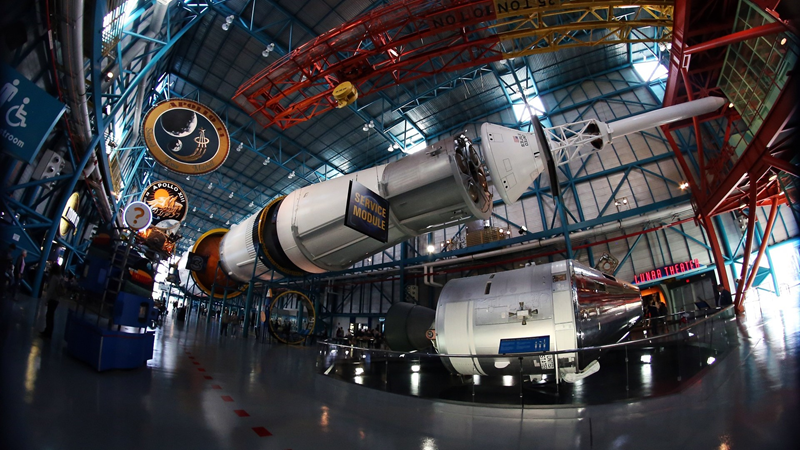
Modern understanding of digital twins may have begun in 1991 but the usefulness of technology that mirrors certain features of a physical entity and simulates its behavior was already known at the time. This is why the simulators developed for the Apollo 13 mission in 1970 are often called the first digital twin.
These simulators consisted of a cockpit and control consoles while everything else about them was simulated with the help of computers. The computing technology at the time was limited. For context, Intel was yet to release the first commercial microprocessor.
Despite the significantly lower computing power, the simulators could receive data from Apollo 13 and show the changes the spacecraft was undergoing after a mission-threatening event. Thanks to this rudimentary digital twin, a solution was found and tested, aiding the astronauts return to Earth.
State of Digital Twinning in 3D Printing
The development of digital twins in manufacturing is still at an early stage. This also applies to 3D printing which may face even more challenges in adopting the technology compared to processes such as assembly.
However, there are a few implementations that showcase the value of merging 3D printers and digital twins. These include:
- A collaboration between Ingersoll Machine Tools and Siemens which has resulted in a large-format 3D printer cum milling and trimming machine that uses digital twinning to accurately control the extruder position and utilize multiple manufacturing processes on the same product.
- A collaboration between WASP and AI Build for yet another large format 3D printer. The digital twin is used for real-time monitoring and thermal simulation.
There is also plenty of research that has revealed the potential of using digital twins to enhance certain aspects of additive manufacturing. You can find out more about the state of digital twinning in 3D printing in this article.
Potential Benefits of Developing Digital Twins For 3D Printers
Better Process Monitoring
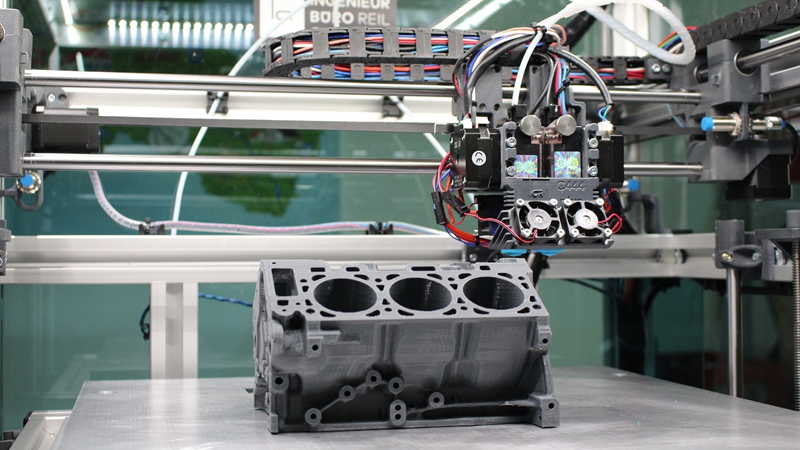
Visual monitoring is currently the most accessible way to track the 3D printing process. This can be in person or via cameras but both options are limited. To get a better understanding of the 3D printing process in real time, it would help to get additional information such as:
- Temperature variations in different parts of the model
- The actual position of the nozzle and printbed in relation to their ideal position
- Amount of material being deposited
- Presence of impurities in deposited material
- Formation of voids and other defects
- Vibration levels in different parts of the printer, etc.
This information can be acquired using digital twins and help improve the conformity of the print to the design. Deviations from ideal printing conditions, defects, and print failures can also be identified early.
Print Setting Optimization
Many mistakes that contribute to print failures are made before the printing starts. Ideal extrusion and printbed temperatures, feed and travel speeds, etc. vary from one print to the next and can be affected by material, part size, layer height, nozzle size, and other factors.
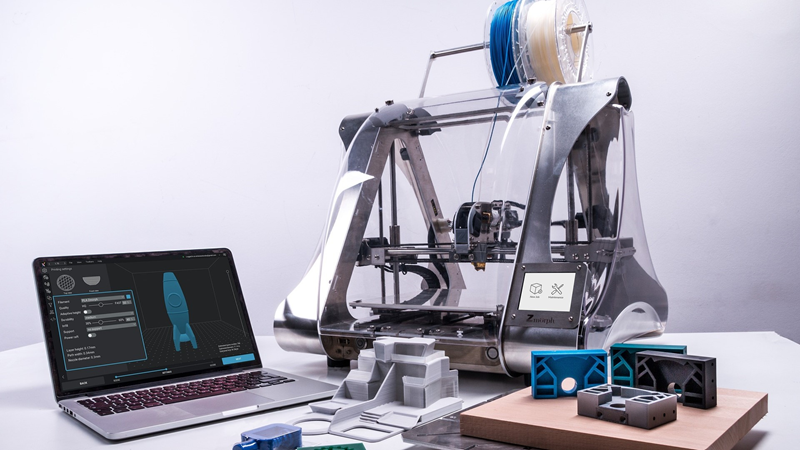
Figuring out ideal print settings often requires experience and a bit of trial-and-error testing. Certain settings are also locked in at the start of printing and can’t adapt to changes.
A digital twin could be used to simulate printing using different settings, allowing users to test different configurations and assess results before the actual printing. Additionally, if incorporated with AI, optimal print settings may be automatically generated, making the process faster and more beginner-friendly.
Design Optimization
Poor part design is a common cause of defects and print failures. A part may look good in the design software but contain features that are harder to reproduce on a 3D printer. Overhangs, for example, require support material which introduces artifacts and other challenges.
Simulating the printing of a part using a digital twin would allow different iterations of the design to be tested to identify the most process-friendly version.
Predictive Maintenance
Time-based maintenance schedules are not ideal for 3D printers. A machine may be subjected to very different workloads from one day to the next since the process favours flexibility in designs.
Digital twins can help to predict when a printer is likely to need maintenance. By comparing live sensor data to historical data, digital twins can identify less obvious signals that historically preceded a failure.
Scheduling
When factory-level twinning is done, scheduling of jobs can be much easier. The digital twin will always have data on which machines are available and how they’ve been set up to identify the best printer for a specific job.
The system may also have a record of pending jobs and levels of urgency to ensure the right machine is available at the right time. When additive manufacturing is used for mass production, this type of system can ensure that orders are processed in time.
Defect Detection and Failure Prediction
Early defect detection is useful in predicting part performance or whether a print should be stopped early. Improved process monitoring using a digital twin can help to identify defects in real-time or the factors that indicate a high likelihood of a defect.
In the same vein, enhanced monitoring can identify signs of impending print failure or poor part formation. Certain temperature variations and poor layer-bed adhesion in a material like polypropylene, for example, may indicate a higher likelihood of print failure in a large print.
Improved Product Quality Plus Quality Control
The quality of 3D-printed parts is often compromised by suboptimal print settings and poor part design. Digital twins that can optimize print settings at the start, or even continuously during the print process will help to improve the quality of printed parts.
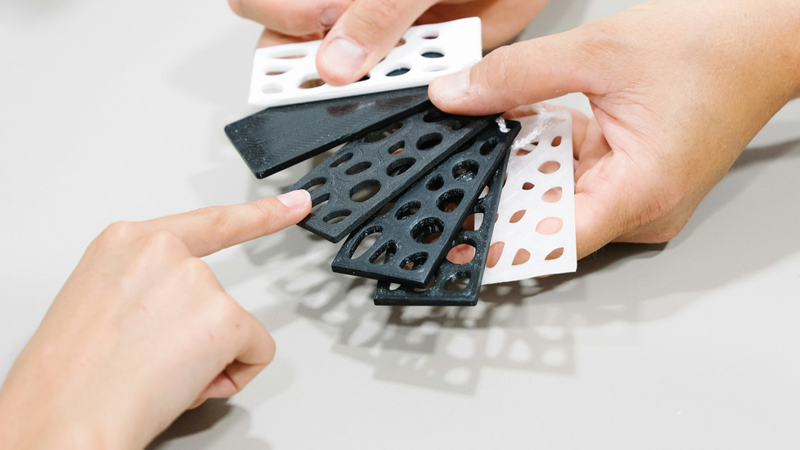
Improved process monitoring will also make quality control faster and more reliable. The manufacture of the part can be monitored from start to finish and any defects identified before the part is off the printbed.
Resource Optimization
3D printing seems relatively affordable when done as a hobby. However, in a commercial setting, the time and material cost of the process is high. This cost is even higher when the printing material is a metal powder or certain polymer types.
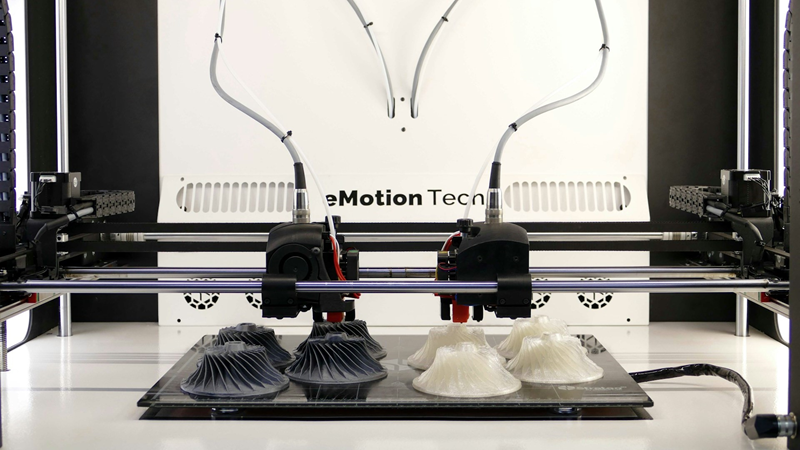
The aforementioned benefits of digital twins in 3D printing will also lower the wastage of time and materials. Fewer resources will spent on trial-and-error testing. Designs will be pre-qualified to ensure maximum compatibility with the process.
When defects that are likely to disqualify a part are detected, printing can be stopped before more material is used. In a busy environment, improved scheduling will maximize the productivity of available machines.
Future Outlook of Digital Twins in Additive Manufacturing
Developing digital twins for additive manufacturing machines would make 3D printing more viable as a manufacturing process. Product quality would improve and certain costs would be lowered. However, certain hurdles must first be overcome to achieve this.
Many of the technologies needed for high-fidelity digital twins for 3D printing are unavailable or very expensive. This includes high-quality sensors and accurate physics-based models. At the very least, this means that developing digital twins for 3D printers will be a costly undertaking. You can learn more about the challenges facing this technology in this article.
Conclusion
According to many experts, digital twins are poised to change many industries including manufacturing. This is because technology may finally be catching up to our lofty ambitions.
In additive manufacturing, there have been a few attempts at incorporating digital twins but the implementation is far from complete and may not be commercially viable yet. However, the research is promising and the story will likely be different in a few years.
Merging digital twins and 3D printing could bring many benefits that would ultimately improve the quality of products and lower production costs. The main hurdle that has to be overcome is the high development cost of this cutting-edge technology.