Additive manufacturing and digital twinning are two of the most promising technologies today. Although neither has had the sort of impact many want to see, combining them to create digital twin-backed 3D printers could make a difference.
Research into using digital twinning technology in additive manufacturing started relatively recently. Despite some successes, the development process is in its early stages and still faces significant hurdles.
In this article, we examine nine key challenges in developing digital twins for 3D printing systems. From technological gaps to high development costs, we’ll see why a commercial implementation of digital twinning in 3D printing is hard to achieve.
History of Digital Twins in Additive Manufacturing
Publications fronting the idea of creating digital twins for 3D printers first appeared around 2017. Therefore, it can be assumed that the research started a year or two earlier. Many early publications focused on theoretical frameworks for developing or implementing these systems.
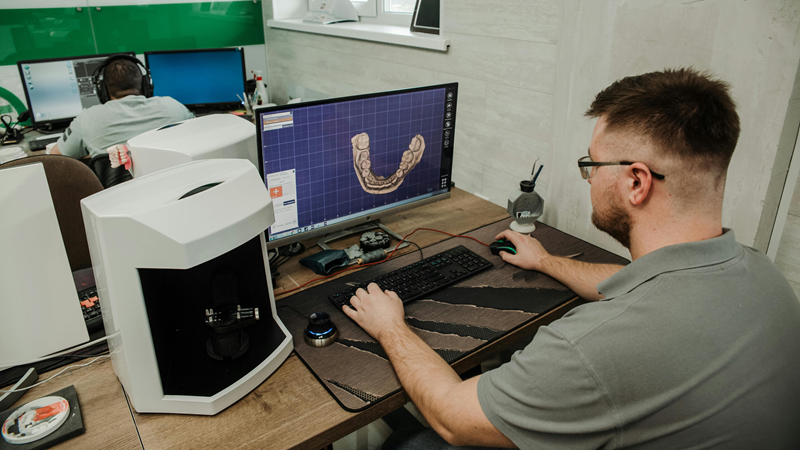
The earliest practical demonstrations of digital twinning in additive manufacturing showed up around 2019. One early example showcased how acoustic signals could be used to non-invasively gather data and reconstruct the printed model in a digital environment.
From around 2021, there has been an explosion of publications demonstrating practical implementations of digital twins and the possibility of using them to solve problems in additive manufacturing including:
- Real-time monitoring
- Fault detection
- Process simulation
- Error correction, etc.
To find out more about the current state of digital twinning in additive manufacturing, check out this article. For a list of academic literature on practical implementations of digital twins in additive manufacturing, you can also check out the literature review section of this paper.
Despite these promising results, there hasn’t been a paradigm-shifting implementation of this concept attached to a commercial product. This is because a commercial implementation will face many challenges.
Challenges of Developing Digital Twins for Additive Manufacturing
Process Simulation
Simulation can be used to predict the behavior of a 3D printer in different conditions or create a visualization that showcases movements of or changes in the printer, among other things. Specific simulations can be used to:
- Show the movement of different parts of a 3D printer in real-time
- Track temperature changes in the deposited material
- Predict the behavior of the 3D printer in specific scenarios, etc.
Simulations can be physics-based or data-driven. Regardless of the approach, simulating an additive manufacturing process is challenging due to the many aspects of the printing process.
For example, to accurately simulate a real-time printing operation, you’ll need to factor in the movements of the extruder and print bed, vibrations due to these movements, movement of the filament through the extruder, temperature changes in the print bed and nozzle, change of state of the material, the effect of environment on temperature/change of state, etc.
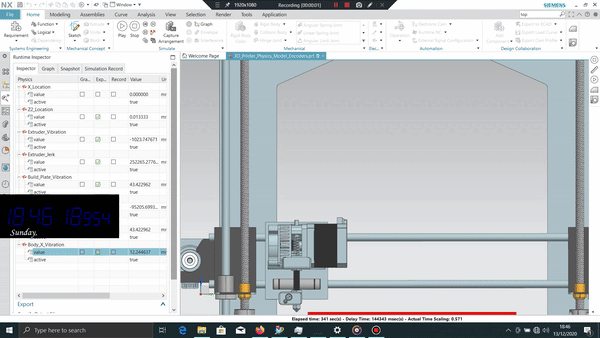
Features such as the change in the shape of molten material are harder to simulate than movement because they’re easily affected by other factors including environment and print settings. More time and resources will be needed to understand and accurately simulate them.
Sensor Technology
Digital twins rely on data from the physical items and the data must be of high quality to ensure high fidelity. Gathering this data requires the use of high-quality sensors but existing sensor technology doesn’t always meet the demands of certain digital twinning applications.
Reliable non-invasive sensors that can gather data without interfering with the 3D printer are not readily available. Some sensors are also fairly expensive, undercutting the commercial benefits of their use. Solutions such as use of virtual sensors are under investigation.
Business Case
Developing a digital twin requires time, money, and expertise. Before committing to such an investment, a business case must be made to justify it. This means demonstrating how the digital twin can generate more revenue for the company developing it.
For the end user, there are many benefits of having a 3D printer with a digital twin. However, the companies that develop these systems also need a strategy to translate these end-user benefits into revenue. This could mean raising the prices of their machines, implementing the digital twin as a SaaS, etc.
Development Costs
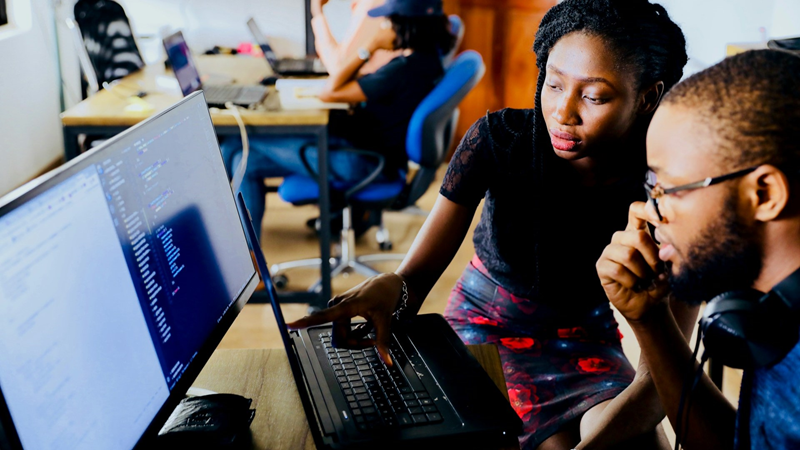
Developing digital twins for 3D printers and turning them into commercial products will require a lot of resources. These resources will be needed for:
- Hiring researchers and software developers
- Licensing patents
- Buying machines, sensors, and raw materials needed for research and development
- Overhead costs, etc.
Not every 3D printer manufacturer today has access to the resources needed to develop a commercial digital twin for their products. Other manufacturers may struggle to convince stakeholders that this investment will pay off early enough to matter.
Compatibility and Customization
Digital twins can be tailored to highly specific items, but this means variations in different products from the same manufacturer must be factored into each product’s digital twin.
A manufacturer with two printer models must develop slightly different digital twins for each. Depending on the level of variation, this could be as much work as developing two completely different digital twins. This is also why independently developing a digital twin that will be compatible with machines from different manufacturers will be a challenge.
However, not every product line requires a digital twin. The technology will likely be limited to high-value products intended for commercial partners who can recapture the value of this investment downstream.
Integration with Existing Hardware and Software
It’s unlikely that a commercial digital twin can be developed that could be fully integrated with an existing 3D printer. For the best results, an additive manufacturing system should be designed and manufactured with the needs and features of the digital twin in mind.
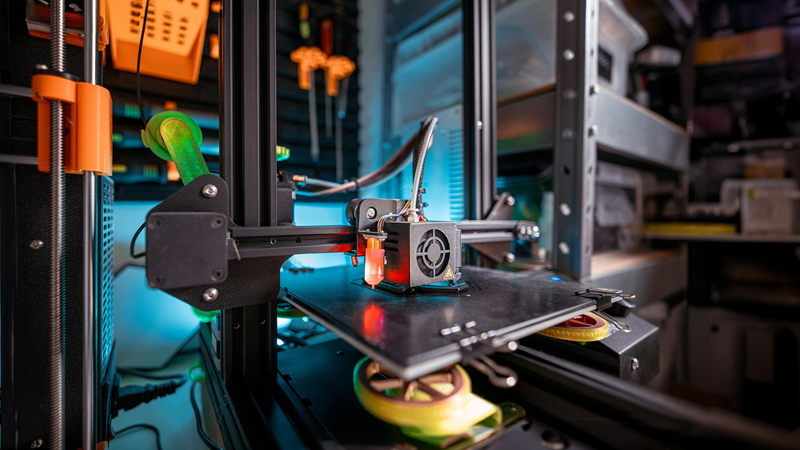
For example, the printer should have features that make sensor attachment easy. Therefore, companies will probably have to redesign their 3D printers and create new product lines.
Data
A lot of data is needed to capture the state of a 3D printer accurately. Depending on the virtual sensors used, a digital twin can also generate a lot of data when simulating the operation of a physical 3D printer.
Additionally, much of the data collected or generated will only be useful for a short period. These factors mean that digital twins inevitably create a data management challenge. The company or customer must have resources to handle this data and policies to manage it to maintain its integrity.
Level of Complexity
The level of complexity of a digital twin for any system contributes to most of the other challenges mentioned in this article. A digital twin with very high fidelity will better capture the state of the physical asset and can be used to make more accurate predictions.
However, high-fidelity digital twins require better process simulation technology and, therefore, more time and resources to develop. Achieving this level of fidelity will require machines that are purpose-designed to accommodate accurate data collection and enhanced machine control.
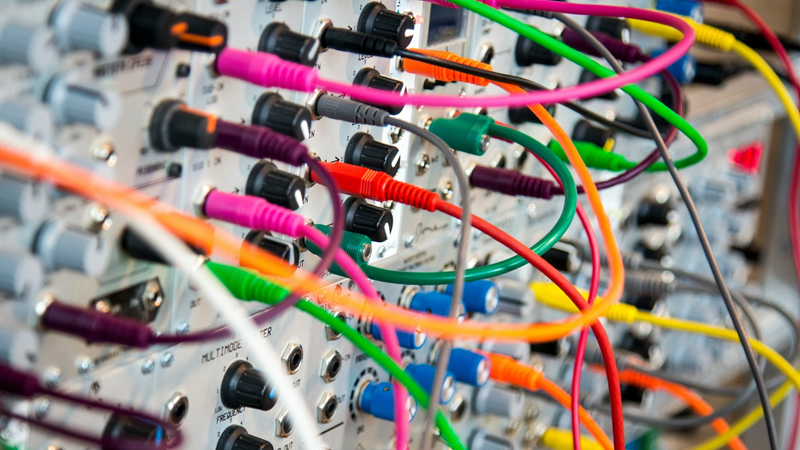
High-fidelity digital twins also generate a lot of data which can be challenging to analyze or manage. Despite all this, the business case of a very complex digital twin may not be significantly better than that of a simple one.
Therefore, identifying the optimal level of complexity is a challenge experts must address to ensure good performance and good returns.
Security
The use of a digital twin can introduce a threat to the users of a 3D printer. If information to or from the digital twin is intercepted, a 3rd party may be able to tell what a 3D printer is used for. A similar hack can also be used to compromise the integrity of manufactured parts.
The possibility of this risk was demonstrated by researchers who were able to reconstruct a printed shape using the acoustic data from the printing operation. 3D printing companies must consider the security risks they and their customers may face when using digital twins.
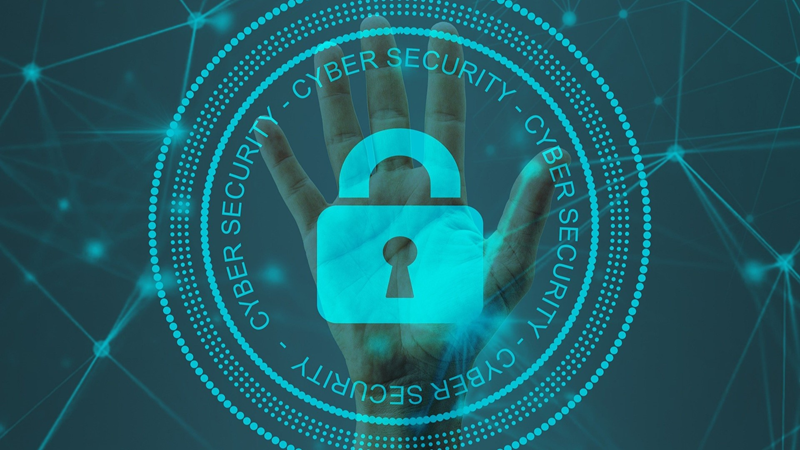
Conclusion
The idea of using digital twins in 3D printing is relatively new but a lot of research has been dedicated to it because of its functional and commercial potential. However, implementing a digital twin for a 3D printer comes with many challenges.
The most significant of these challenges are the technologies that are yet to be developed or can’t yet be deployed affordably. However, even after these are solved, companies will need strategies to ensure the development is feasible and to handle the data management and security problems that will follow.
None of the challenges facing the development of digital twins for 3D printers is likely to be fatal. In the real sense, these challenges merely demonstrate that these systems demand too much and should only be developed where they can create real value.